Plastics Molding and Processing
KUS is adept in various plastic molding and processing techniques, as these skills are the heart of our business. KUS is equipped with more than 200 professional and accredited mold designers and manufacturers. For over 30 years, KUS has perfected many molding methods using our world-class equipment, including injection molding, blow molding, and rotational molding. Discover how excellence in manufacturing can benefit you and explore our range of quality molding services.
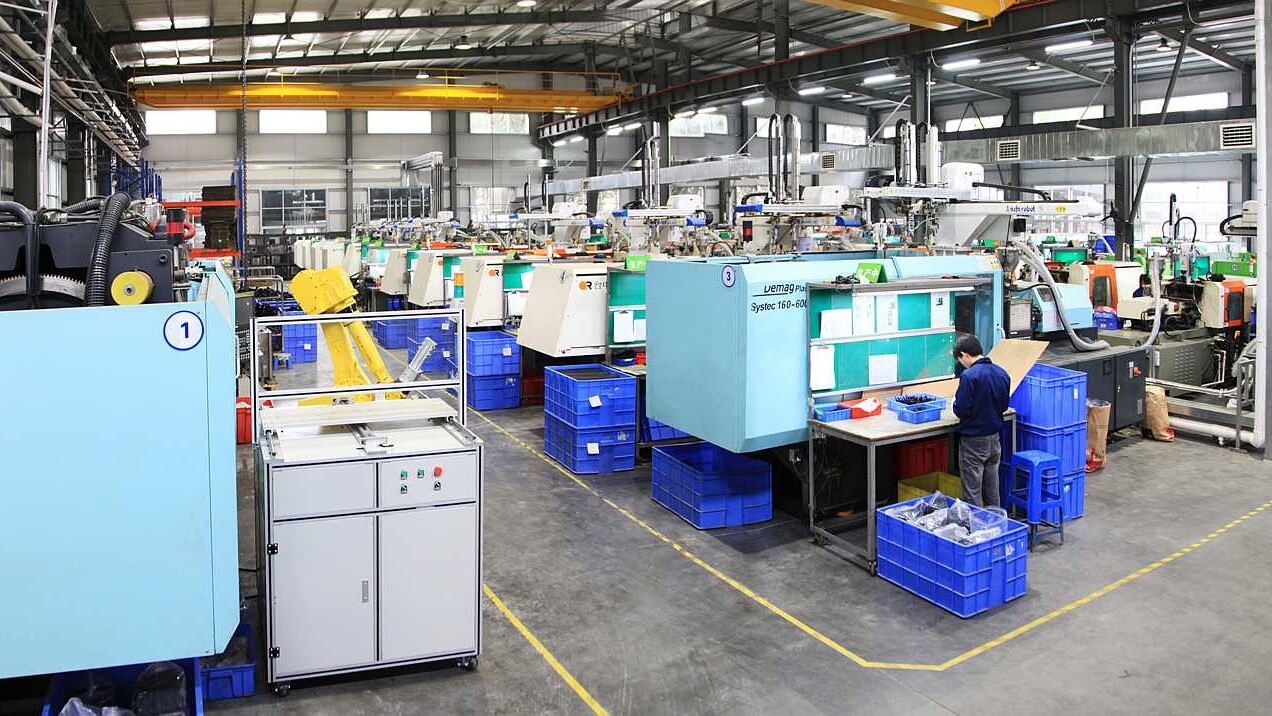
Injection Molding
KUS has more than 300 injection molding machines throughout the central feeding system to accurately control the temperature and humidity of raw materials to ensure product quality and molding size.
KUS uses injection molding to produce solid parts, such as fuel level sender heads and other accessories. Injection molding can be executed with a variety of different materials, and KUS has the experience to know which options are best for each product. Using automatic central feeding we turn the selected raw materials into a semi-finished product. KUS heats plastic to a liquid form and feeds it into an injection molding screw where it is then injected into a cavity through a pressurized system. Through this process a part is formed, that part is then cooled and ejected from the cavity. KUS leverages vibration, ultrasonic, and hotplate equipment within the process to produce the product. Regulating temperature and humidity in our facility benefits our injection molding process. We manufacture in a controlled environment to help prevent defects due to changes in outside conditions.
Blow Molding
KUS has 42 sets of blow molding machines with an annual output of 2.3 million and a tank volume between 5L to 300L.
KUS uses blow molding to produce hollow parts, such as our DEF tanks. This molding technique not only makes manufacturing complex parts possible, but offers the advantage of quick production time as well. KUS uses either HDPE plastic or LLDPE plastic, depending on the application, molding it into various shapes and blowing it with compressed air into the tube billet to fill the mold cavity. The blow molded part is cooled and then ejected from the cavity. Rapid blow mold design and manufacturing is made possible through our automatic mixer feeding system, as well as our professional tank design team.
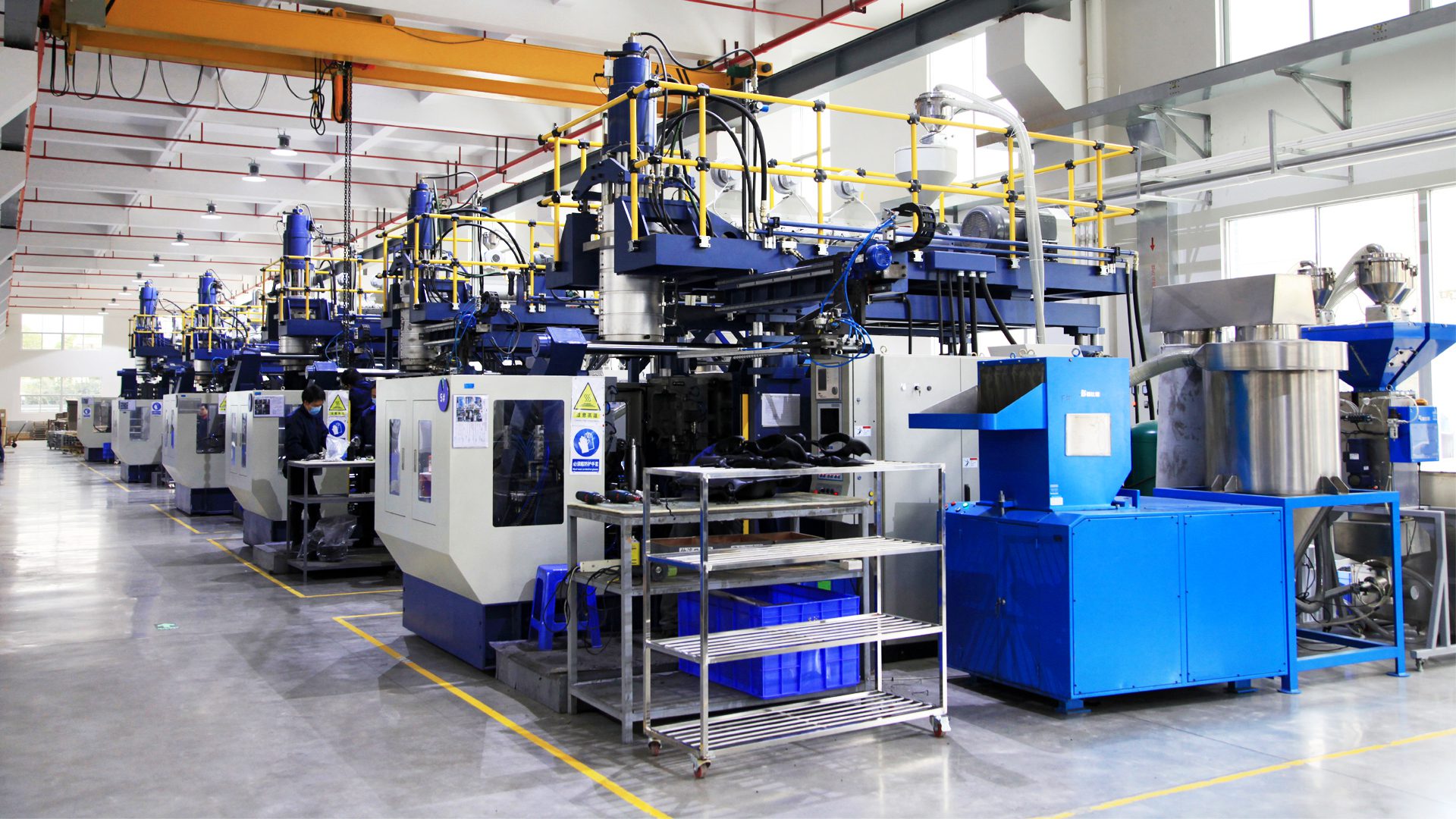
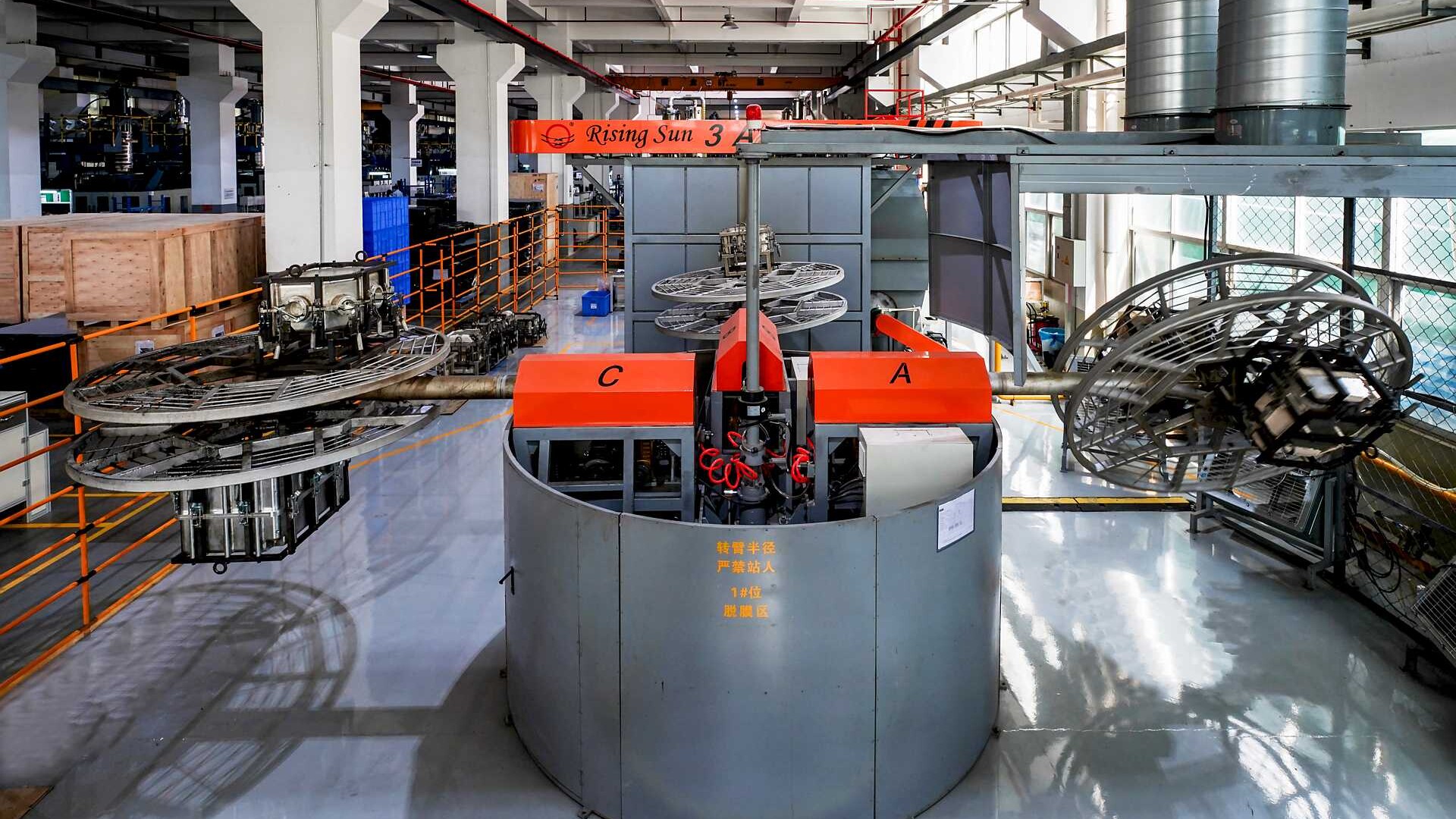
Rotational Molding
KUS has 7 sets of rotational molding machines with an annual output of 1.75 million and box volume between 5 to 500L.
Rotational molding is a manufacturing process that is also known as Rotomolding. This plastic molding technique produces a range of various products with hollowed centers. KUS uses raw materials that are poured into the mold cavity, this mold cavity is then rotated and heated to form the desired shape. The rotational molded part is cooled and then ejected from the cavity. Rotational molding can accommodate varying wall thicknesses for a number of different applications, in our case, DEF tank manufacturing applications. The advantage of roto molding is that it allows for larger volume tank sizes and can produce more complex tank geometries.
For more information regarding computer-aided engineering (CAE) and how it might be used to manufacture products for you,
contact our team today!