The main features people look for in a DEF tank are durability, reliability, customizability, and a fair price. Thankfully, the market has continued to innovate over the years, and there are more options available to replace your vehicle’s DEF tank than ever before.
Outside of deciding which DEF tank manufacturer you want to work with, you may also be wondering which type of material is the best for DEF storage? Let’s explore your options.
What Are the Most Common DEF Tank Materials?
The most commonly used materials to construct DEF tanks are metal and polyethylene — a commonly used plastic material. More specifically, DEF tank manufacturers rely on stainless steel, coated carbon steel, or high-density polyethylene (HDPE) containers for DEF storage. You should typically avoid tanks made of aluminum or lower density plastic, as they can contaminate the DEF solution
In the beginning, most DEF tanks in the US were made of plastic, but over time many vehicles began incorporating some type of steel-coated DEF tanks in their designs. These DEF tanks were sturdy and dependable, however they were also very heavy
With stricter regulations from the Environmental Protection Agency, vehicle and equipment manufacturers now have to make all their output more environmentally friendly and fuel-efficient. As a result, many manufacturers have switched to using high-density polyethylene (HDPE) DEF tanks. HDPE tanks prove to be just as long-lasting, if not more so, than steel tanks.
So how do we determine which material is better for your DEF tank assembly?
DEF Tank Material Pros and Cons: Polyethylene vs. Steel
There are rarely any flawless technological advancements. Let’s examine the two most common DEF tank materials used today and their respective pros and cons.
Benefits of High Density Polyethylene DEF Tanks: Durability, Moldability, Weight
Polyethylene tanks have their fair share of upsides when compared to steel tanks. For starters, polyethylene tanks are more crash-resistant than steel tanks. This is because polyethylene tanks are seamless and lack vulnerable seam areas that metal tanks have. Additionally, polyethylene tanks can deform and then rebound back to shape. This is opposite of steel tanks which deform permanently upon collision, often breaking along the seams where the shock occurs.
Another pro of high-density polyethylene DEF tanks is their moldability in comparison to metal tanks. The nature of polyethylene as a material allows it to form into complex shapes. This gives engineers a much greater ability to design the internal structure of vehicles. Steel tanks, on the other hand, are rigid. This requires creating the underlying specs of the vehicle around the shape and weight of the fuel tank itself, which can lead to unforeseen design complications.
Yet another benefit polyethylene tanks have over steel tanks is their weight. Polyethylene fuel tanks are roughly 20%-30% lighter than steel tanks on average, which can help tremendously with how many miles per gallon your vehicle gets. This also leads to easier compliance with federal regulations, which mandate all automobile manufacturers to hit a certain level of performance per mile to sell their cars on the marketplace in the United States.
Benefits of Steel DEF Tanks: Fire Resistance, Affordability, Recyclability
For starters, steel-based DEF tanks are more resistant to fire damage. According to the National Fire Protection Research Foundation and Factory Mutual Research Corporation, polyethylene tanks storing flammable or combustible liquids in general-purpose warehouses can fail abruptly when exposed to a small fire. These fires, in particular, can lead to dangerous situations partly because spill fires can often overpower conventional sprinkler systems. The same test on steel tanks, however, had no such issues. With that in mind, these findings have led some people to stick with steel containers over polyethylenes for safety and fire insurance cost reasons.
That said, as long as you are storing DEF in the proper conditions using HDPE, you can counter many of the risks associated with fire exposure and combustion that polyethylene containers present. You should also note that DEF itself is a nontoxic and nonflammable solution.
The next benefit of steel or coated carbon steel DEF tanks is that they can potentially have lower production costs depending on the metal used. The metalworking industry is very mature and has a firmly established global supply chain compared to the polyethylene industry.
As a result, metal tanks can be cheaper than their polyethylene equivalents. For example, coated carbon steel DEF tanks fall into this category, with stainless steel being the notable exception.
Another benefit of steel tanks is their recyclability. In large part to how metalworking works, most steel is easily recycled and repurposed. In fact, 70-80% of a typical passenger car consists of recoverable steel and iron. This is in contrast to many polyethylene-based products, where roughly 30% of polyethylene material becomes industrial waste. There are exceptions to this rule, however, as HDPE polyethylene tanks are easier to melt and recycle than most other plastics.
Polyethylene vs Steel DEF Tanks: A Final Comparison
Steel DEF Tanks:
Benefits:
- Cheaper in bulk for most metals
- Easy to recycle
Disadvantages:
- Not crash resistant
- Inflexible design
- Heavier
High Polyethylene DEF Tanks
Benefits :
- Crash resistant
- Flexible design
- Lighter
Disadvantages :
- Price of materials may fluctuate
- Difficult to recycle
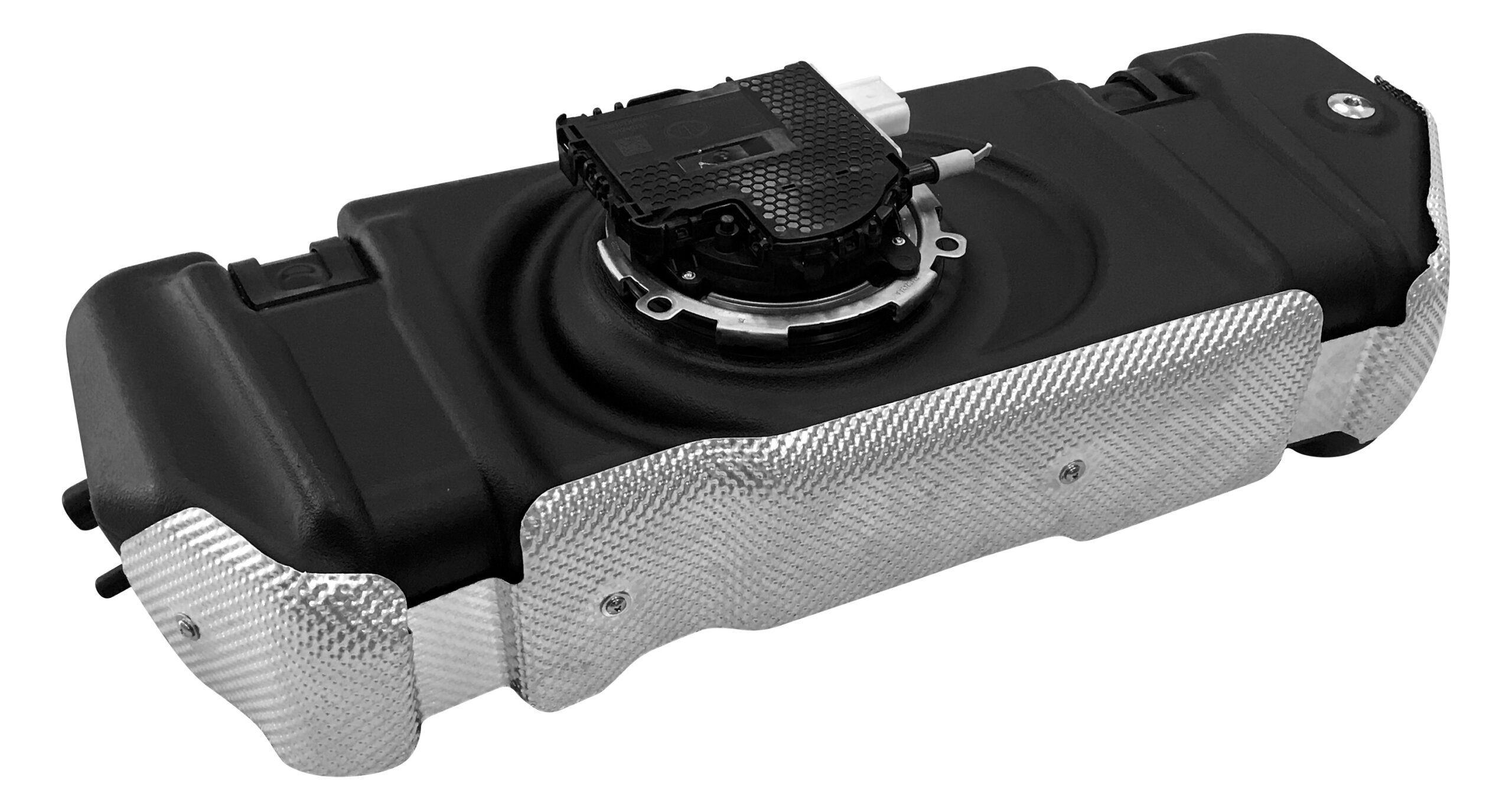
Shared Strengths Between the 3 Materials
High-Density Polyethylene (HDPE), Medium-Density Polyethylene (MDPE), and Linear Low-Density Polyethylene (LLDPE) share some common ground. All three materials have good insulation, are moistureproof, and have anti-seepage properties. Additionally, they are all nontoxic, tasteless, and odorless.
LDPE's Strengths
HDPE has strong anti-corrosion properties. HDPE can also aid dissolution of strong oxidants, such as concentrated nitric acid. It can also aid in the dissolution of acid-base salts and organic solvents like carbon tetrachloride.
HDPE’s Weaknesses
HDPE’s aging resistance and environmental stress cracking performance are not as good as LLDPE. In particular, thermal oxidation will diminish performance.
MDPE'S Strengths
MDPE is the lightest variety of polyethylene with good extensibility, meaning it stretches and molds more easily. MDPE also has great electrical insulation and chemical stability properties. In addition, MDPE has substantial processing performance and low-temperature resistance, down to -70 degrees Celsius or -94 degrees Fahrenheit .
MDPE's Weaknesses
MDPE’s mechanical strength, moisture barrier, gas barrier, and solvent resistance are poor. Its impermeability coefficients, heat resistance, and solar aging resistance are also poor.
LLDPE's Strengths
LLDPE has high strength, toughness, rigidity, heat resistance, and cold resistance. It also offers resistance to environmental stress cracking and tear resistance. LLDPE resistance to acids, alkalis, and organic solvents is also strong
LLDPE's Weaknesses
LLDPE can swell if it’s in contact with benzene for an extended period of time. LLDPE will also become brittle when in contact with HCL for a long time.
Why Does KUS Use High-Density Polyethylene?
Ultimately, KUS uses High-Density Polyethylene (HDPE) when creating DEF tanks. The reason for this is because manufacturers are requesting more customizable DEF tank options.
In addition, polyethylene tanks are often more manageable for an organization’s engineers to work with in exchange for the benefits they provide. This is especially true when comparing steel tanks’ respective strengths and weaknesses. Furthermore, KUS manufactures and handles the whole DEF tank assembly in-house, preventing delays caused by outsourced teams.
At KUS, our engineering and design teams have over 10 years of experience designing custom DEF tanks and complete tank assemblies for SCR system integrators and vehicle and engine OEMs. In addition to its custom solutions, KUS also offers standard, ready-to-market DEF total tank assemblies ranging from 16L to 80L. This provides our customers with a variety of options.
View our main DEF product offerings in our online shop or contact us for more information.